The revolution will be printed
Building for Humanity wanted to prove that there was a simple solution to the housing crisis. Their answer: 3D printing.
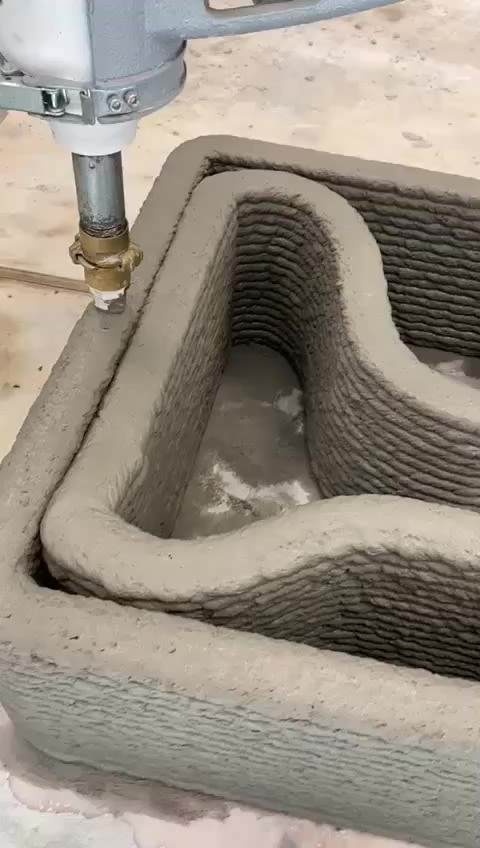
Photos courtesy of Building for Humanity
Photos courtesy of Building for Humanity
Britain’s housing crisis has reached critical levels. A shortfall in social housing and rising construction costs has made affordable homes increasingly elusive.
But a new and rapidly developing technology could offer a solution - 3D concrete printing.
One not-for-profit housing company called Building for Humanity is constructing Europe's largest ever 3D concrete printed social housing development in Accrington, and they believe this technology could offer a solution.
By capitalising on the latest concrete printing technology they aim to redefine how affordable housing is constructed by building 46 homes, a community centre, and a shared green space.
The £6 million Charter Street project will be Europe’s largest stand-alone 3D printed residential development which aims to break ground between September and November this year.
Building for Humanity commercial manager Iain Hulse said: “The technology has provided the opportunity to do exactly what we want to do but quicker and a lot more cost effectively.”
With a philosophy based around achieving greater affordability, sustainability and efficiency within the housing sector, Building for Humanity aims to add social value, training and employment opportunities for its 150 residents.
Its benefits include reducing labour costs, quicker construction and a reduction in waste, with the company aiming to save 30% on production time and costs.
Hulse added: “But the aim of this is not just to utilise the technology and promote it but also to show how easy it is to solve an unsolvable social housing problem.”
Local action group Social Homes for Manchester uncovered that 506 of the 23,264 homes built in the city between 2012 and 2022 were social housing, and the issue became a central part of Andy Burnham's election campaign promising 10,000 new council homes by 2028.
One solution could be using brownfield sites.
3D concrete printed developments can be produced on any of the 33,710 commercially unviable sites in the UK due to their ability to adapt to the complex environments and print directly on site.
This can therefore mitigate issues faced by traditional construction methods when dealing with existing structures or environmental concerns.
And this is just one example of the advancements in the technology.
3D printing has been around since the 1980s, but only recently has its true capabilities been uncovered and experts believe research can create a real possibility of net zero ambitions.
Research into the development of advanced materials at PrintCity in Manchester is leading the way and offers a glimpse into the sustainable future of 3D printing and its applications.
The company won the 3D printing industry award for research team of the year, outperforming competitors from Harvard University and Zurich Institute of Technology.
Technical specialist Nick Hurst has led the concrete printing project. In collaboration with industries in France, Germany, the Netherlands and Belgium, he aimed to develop a sustainable mortar by recycling construction waste which can be crushed down into larger more manageable waste.
The bi-product is a fine aggregate, which would otherwise go to landfill, and Hurst uses it as a replacement for sand.
Research by the United Nations uncovered that humans extract 50bn tonnes of sand and gravel each year, enough to build a road that circled the earth 40 times.
The hope is that by recycling concrete, 3D printing can spearhead a green revolution and remove the need to use the world's second most extracted resource and therefore offering a realistic possibility of hitting net zero.
The technology is already being used in major infrastructure with plans for the HS2 line to use computer-operated robots to 3D print in physically restricted areas and halve carbon usage.
Free-standing recycled concrete plant pots made at PrintCity
Free-standing recycled concrete plant pots made at PrintCity
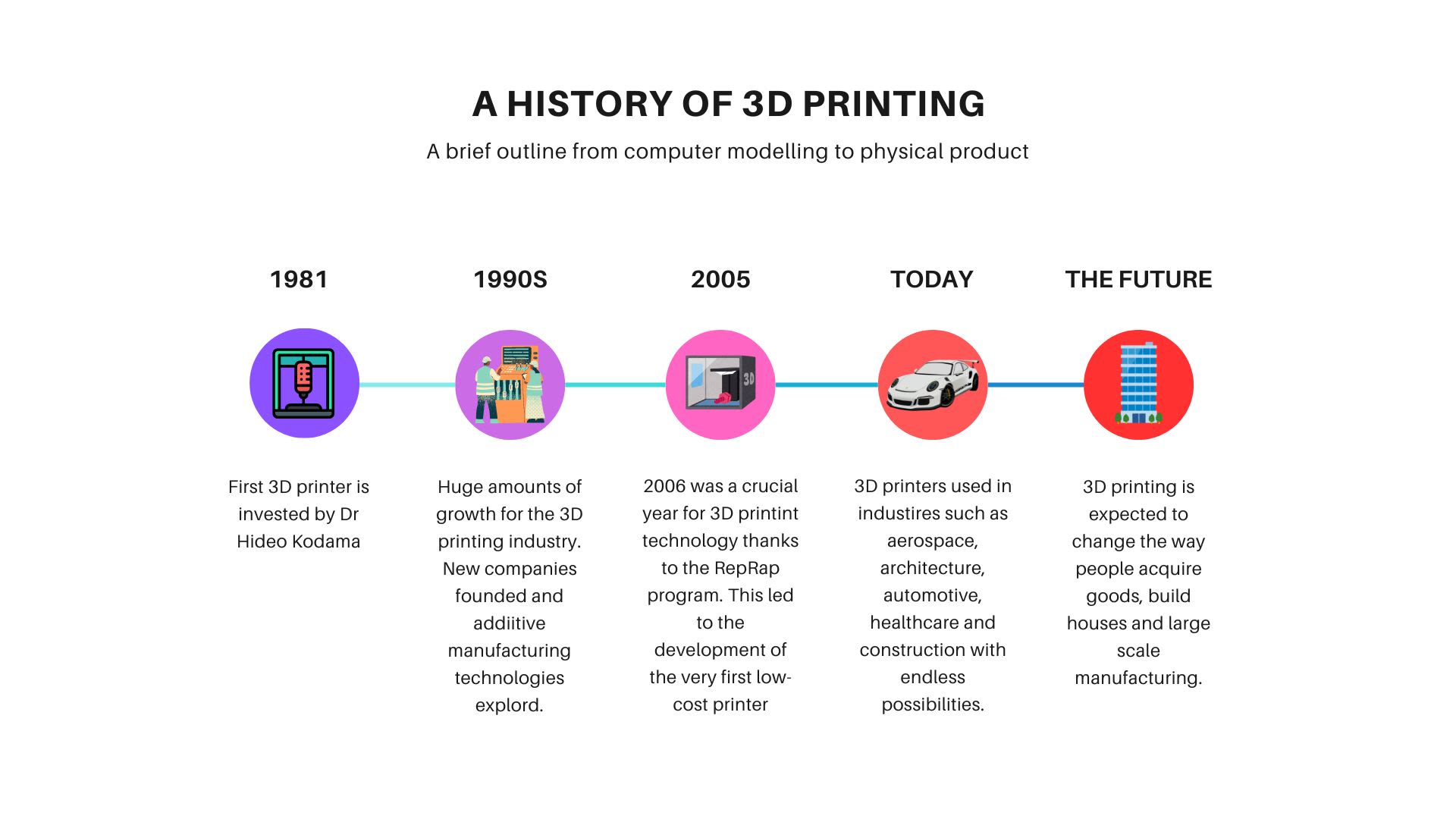
Mark Chester, Product Development Specialist talks about the benefit of localising production.
Mark Chester, Product Development Specialist talks about the benefit of localising production.
However, it is not just the construction industry which could benefit from a surge in 3D printing technology.
Hurst added: “3D printing can be used in a lot of industries and this is part of our philosophy.
“It doesn’t matter if you are from engineering or textiles, whatever your background there is some application to 3D printing.”
In a bid to rebuild the British manufacturing industry, the government commissioned the Made Smarter review in 2017.
The think tank found 3D printing could boost development and act as a resource hub for small and medium sized enterprises.
As a result, localised production became an essential cog in the 3D printing machine.
Product Development Specialist Mark Chester said: “If you produce in-house or down the road that carbon footprint of your product should reduce a lot.
“The best projects we have worked on are where we see significant changes in the companies whether that be a significant reduction in money, or other added value in terms of reducing the amount of Co2 they are producing, or being able to go to market a lot quicker.
“That is where we see real benefit.”
Therefore, by harnessing the power of 3D printing technology, experts believe that Britain has a unique opportunity to address its housing crisis, reduce environmental impact and bolster local economies through an efficient manufacturing process.
They are also hopeful that this potential lies in the capacity to embrace these advancements and offer sustainable as well as affordable solutions for the next generation.
Examples of the unique designs created by 3D printing.
Examples of the unique designs created by 3D printing.
Through scanning technology 3D printing has allowed to create a hand-on experience in museums.
Through scanning technology 3D printing has allowed to create a hand-on experience in museums.